Strategies for Enhancing Manufacturing Efficiency and Quality Control
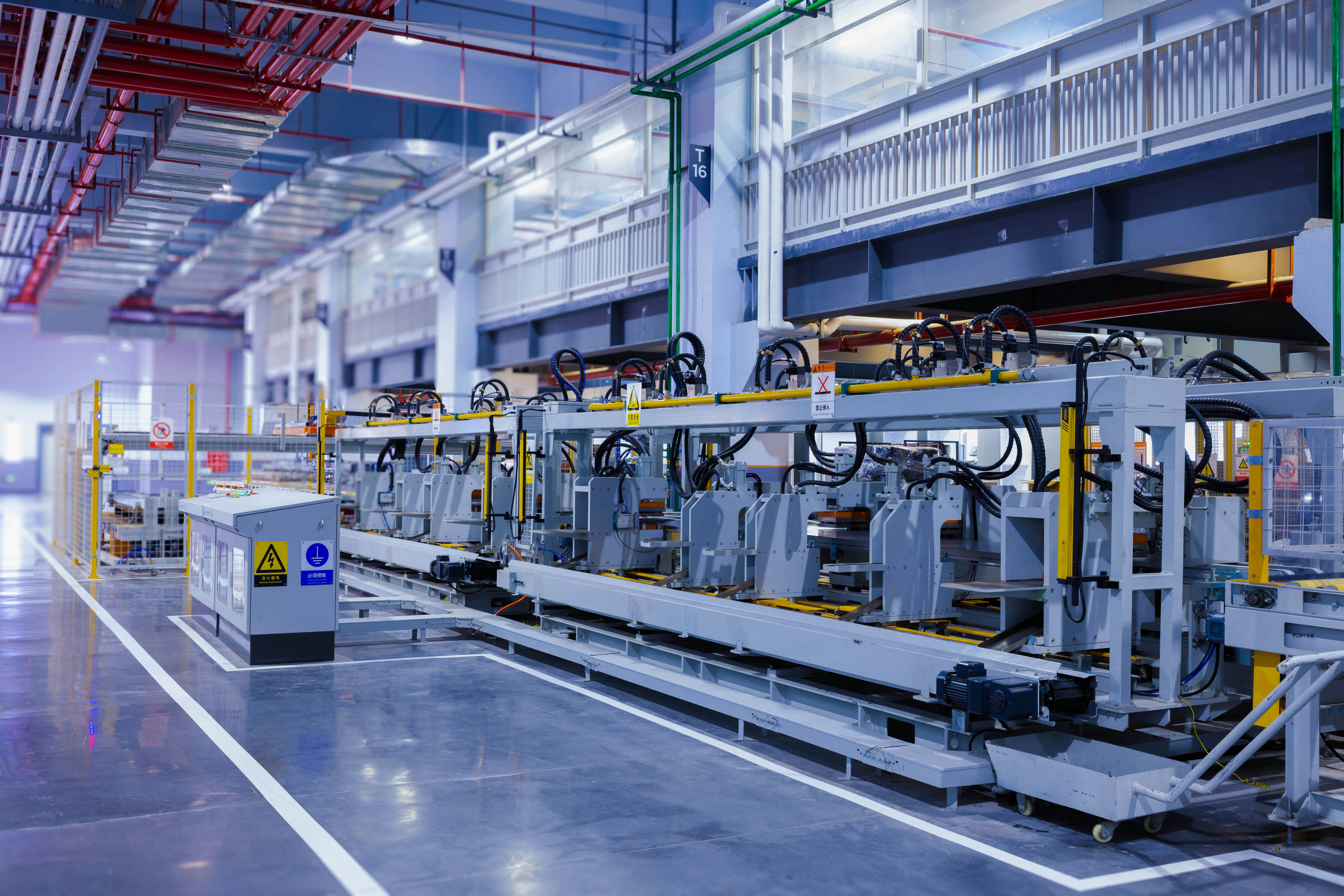
Ari Philippides, former Head of Manufacturing at BMI Group and SMARTKEM, and an expert in Lean and OPEX methodologies, has vast experience in transforming manufacturing processes. His approach to improving efficiency focuses on integrating stakeholder confidence, streamlining operations, and leveraging data to optimize decision-making. In this detailed interview, Ari explores key strategies that have helped him successfully reduce waste, improve product quality, and maintain safety standards while driving cost-efficiency in complex manufacturing environments.
Establishing Stakeholder Confidence for Effective Problem-Solving
Ari emphasizes that success in manufacturing begins with confidence-building among all stakeholders – be it leadership or the operational team. Establishing trust is key to defining problems accurately and aligning everyone toward common objectives. “It’s essential to engage both those who set the objectives and those whose engagement is critical to implementation”, says Ari. He utilizes Value Stream Mapping (VSM) and Process Mapping as foundational tools to ensure clarity in problem definition, helping teams focus on the root causes of inefficiencies.
Through these approaches, the goal is to gather actionable data that illuminates the constraints in the system, whether they are technical, procedural, or human related. “Often teams tend to mix up VSM and Process Mapping, but both have distinct purposes”, Ari adds. “VSM helps us pinpoint where value is lost, while Process Mapping provides a visual flow of all operational steps, identifying bottlenecks”. The process aims to not only meet production targets but exceed them by removing inefficiencies and eliminating potential roadblocks.
Defining and Prioritizing Solutions: The Role of Lean Tools
Ari stresses the importance of using traditional Lean tools, such as the 7 Wastes (MUDA) and OEE, to prioritize solutions that align with production goals without creating new bottlenecks. These Lean tools guide the team in identifying areas where physical waste is generated – whether due to overproduction, defects, or time lost during equipment changeovers.
By focusing on both internal waste within the factory and customer-related waste caused by defects, Ari ensures that solutions are sustainable. He elaborates on the importance of eliminating customer-related waste through methods like Variability Reduction, often achieved by applying Lean and Six Sigma methodologies. “Reducing variability in production ensures that we not only increase efficiency but also deliver consistent quality to customers”, he says.
Integrating Lean Principles: GEMBA and Daily Operations
Daily operations are where Lean principles come to life for Ari. He advocates the use of GEMBA walks, where he personally visits the production floor to observe and engage with operators. “GEMBA is about being present where the actual work happens”, he explains. “It’s an opportunity to address inefficiencies in real time, resolve immediate issues, and reinforce the importance of safety and quality standards”.
A key focus of these walks is to review the previous day’s performance and address any shortcomings. Operators are encouraged to log data at hourly intervals, tracking both positive and negative deviations from the targets. This real-time tracking allows management to implement corrective actions promptly. “It’s not just about pointing out issues but ensuring that they are resolved effectively”, Ari stresses. Root cause analysis, particularly through the 5 Why method, helps his team dig deeper into recurring problems and find lasting solutions.
Maximizing OPEX Methodologies: Case Study from INNOVIA Films
One of the most successful applications of OPEX in Ari’s career was at INNOVIA Films, where he led a project aimed at increasing production capacity and financial returns by reducing waste. “The VSM revealed a series of physical losses across several operational steps, particularly in the coating area, which was both the bottleneck and the site’s highest value-adding process”, Ari recalls.
His team worked to reduce variability in the startup process for each reel of film, which was causing excessive waste. Standardizing this process across shifts increased consistency and reduced waste by 0.5%, a small percentage with significant financial implications. “The lesson here was that even small reductions in waste, when targeted correctly, can lead to substantial revenue gains”, he notes.
Another area of focus was reel turning speeds during the splicing process. “We discovered that slowing the machines to match the speed of the least waste-producing machine led to improved product quality and less material waste”, Ari shares. This optimization not only increased product yield but also reduced customer-related defects, as the final product became more consistent.
Overcoming Resistance to Continuous Improvement
When it comes to implementing continuous improvement initiatives, Ari identifies human resistance as one of the greatest challenges. “People often feel threatened by outsiders or fear losing control over their areas of responsibility”, he explains. To overcome this, Ari adopts a humility-driven approach, where he listens closely to the concerns of both the team leaders and the operators.
“Gaining their trust is crucial,” he says. “Once people realize that the goal is to improve the process, not to undermine their expertise, they become more engaged and eventually empowered”. By fostering a culture of inclusion, where every team member has a stake in the outcome, Ari ensures that continuous improvement becomes a shared responsibility rather than a top-down mandate.
Balancing Cost Reduction with Safety and Quality
Ari is adamant that cost-cutting must never come at the expense of safety or product quality. “It’s both unethical and illegal to make operational changes without considering their safety implications”, he asserts. Any proposed changes must undergo a thorough risk assessment, involving all stakeholders who will be affected by the change. This ensures that risks are minimized and that safety standards are not only maintained but strengthened.
In Ari’s experience, involving the team in these assessments builds a sense of ownership and accountability. “When people see that safety and quality are prioritized, they’re more likely to support cost-saving measures because they trust that these changes are being made responsibly”, he explains.
Cross-Functional Collaboration: Aligning Production, Quality, and Supply Chain Teams
One of Ari’s strengths is aligning cross-functional teams—such as production, quality control, and supply chain—towards shared operational excellence goals. “Collaboration is key”, he says. “You need buy-in from every department, and that begins with clear communication from the top leadership”. Ari points to his time at Astrocast, where he worked to unify these teams around the common objective of improving customer delivery and maintaining production efficiency.
To facilitate this collaboration, Ari ensures that all teams participate in GEMBA walks and other daily operational meetings. This inclusive approach not only fosters alignment but also ensures that every department understands its role in driving overall business success.
Leveraging Data and Technology for Operational Excellence
Data is at the heart of Ari’s decision-making process. He emphasizes the importance of digitizing data collection and leveraging automation to streamline operations. “The integration of data from multiple sources allows us to identify trends and address inefficiencies more quickly”, he says.
At Forbo Flooring, Ari used data-driven insights to resolve long-standing issues with color consistency. “Traditionally, color inconsistencies were managed through manual intervention, but with better data and automation, we were able to find a more reliable solution”, he explains. This shift from opinion-led to data-led decision-making allowed the company to significantly improve product quality while reducing rework and waste.
Training and Upskilling the Workforce
Ari believes that ongoing training is essential for maintaining alignment with Lean and OPEX methodologies. He ensures that any process changes are documented as Standard Operating Procedures (SOPs) and that these are integrated into a formal training program for all operators. “Competence is measured not just by following the procedure, but by understanding why it’s important”, he says.
By using Statistical Process Control (SPC) charts, Ari reinforces the importance of compliance and corrective actions. This ensures that the workforce remains engaged and aligned with the broader objectives of continuous improvement.
Critical Factors for Success in Modern Manufacturing
In today’s fast-evolving manufacturing landscape, Ari identifies three critical factors for success: automation, data collation, and effective maintenance. However, he also stresses that the human element is equally important. “Success in manufacturing starts with people”, he says. “Leaders must demonstrate respect, listen to their teams, and act on their concerns. This creates a cycle of engagement, empowerment, and continuous improvement”.
For executives navigating this landscape, Ari’s advice is clear: “Invest in technology, but never forget that it’s the people who make the difference. Empower them, and you’ll see the rewards”.